A Region on the Verge of Discovery
The NY tri-state area pulses with scientific progress and energy, changing the world far beyond its borders.
Published June 1, 2013
By Steven Barboza
Academy Contributor
The nursery rhyme about London Bridge falling down gives a fair assessment of the fate of bridges. Patch them up with wood and clay, and the wood and clay will wash away. Iron and steel would fare better, but eventually these bridges will bend and bow. But what about plastic?
Structural plastic—the stuff of recycled milk cartons, detergent bottles, and car bumpers—is actually a bridge-builder’s dream. It can be molded into T-beams then bolted into I-beams that are eight times stronger than steel at one-eighth the density. It can be drilled, screwed, sawed, pinned, and even sprayed with a fire-retardant coating.
Theoretically, a plastic George Washington Bridge is possible. “There’s no technical limit to how big a beam we can make out of plastic. All you need is bigger beams to make bigger bridges,” says Tom Nosker, professor of materials science and engineering, who developed structural plastic at Rutgers University’s Advanced Polymer Center in NJ.
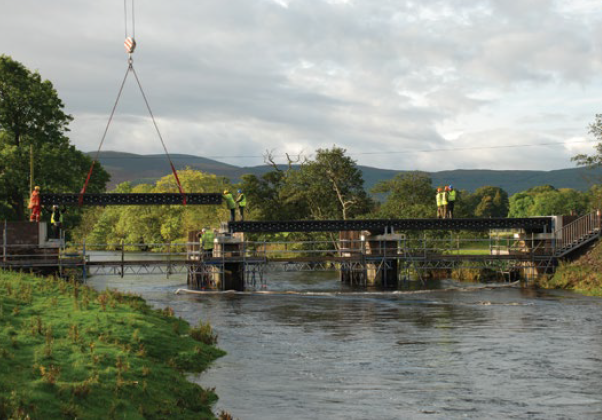
The Material Advantages of Plastic
The engineering lesson is elementary. Even sturdy wooden or cement and steel bridges erode given enough time, traffic, and exposure to wind and weather. Plastic beams will not buckle; they’re impervious to rot; and they’re eco-friendly, providing a novel use for mountains of discarded milk containers.
But there’s a broader lesson here: the entire New York tri-state region is a kind of science and technology Grand Central, where researchers bustle to push back the boundaries of possibility. Structural plastic is only one of the region’s thousands of innovations bound to affect our lives in extraordinary ways in the not-so-distant future.
An incredible array of area research universities are bristling with a spirit of invention that extends New York’s science ecosystem into a much larger footprint—creating an entire region of unparalleled scientific excitement.
A New Frontier in Manufacturing
Connecticut is brewing a latter-day industrial revolution of its own, as it paves the way for digital manufacturing. The University of Connecticut (UConn) has built a sort of factory of the future—one of the most advanced additive manufacturing centers in the nation. Additive manufacturing is a breakthrough method of making things—from flight-proven rocket engines to individually tailored hearing aids. Instead of using lathes, drills, molding machines, and stamping presses, it uses software and digital 3D printers that build items layer by layer. There’s no waste, molds, or assembly of intricate parts
The new Pratt & Whitney Additive Manufacturing Innovation Center, a partnership of UConn and Pratt & Whitney, is the Northeast’s first such facility to work with metals. Techniques developed here might one day empower small and medium-sized firms and entrepreneurs to launch novel, incredibly complex products quickly, profitably, and more flexibly than ever, with minimal manual labor.
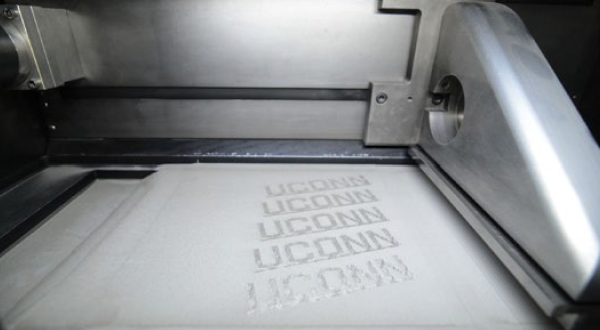
Imagine a new generation of intricate, lightweight, and durable custom products—printed in cost-efficient home factories.
At UConn’s center, which houses 3D manufacturing equipment and rapid prototyping technologies, two high-powered electron beam melting machines and lasers repeatedly melt layer upon layer of powdered material, such as titanium, into a single solid piece. The items are built to the exact specifications dictated by a 3D computer assisted design (CAD) model. Engineers are using the center to develop advanced fabrication techniques for production parts in aerospace, biomedical science, and other industries.
“The new center will allow us to push into new frontiers of manufacturing and materials science while training a new generation of engineers in some of the world’s most sophisticated manufacturing technology,” says UConn President Susan Herbst.
Bringing Cybernetics to Life
Scientists at Princeton University are also using 3D printing tools, not to crank out jet engines, but to print a fully functional organ—a bionic ear so sensitive it can tune into frequencies far beyond the limits of human hearing.
The bionic ear is a bold mixture of electronics and tissue. Researchers, led by Michael McAlpine, an assistant professor of mechanical and aerospace engineering, used an ordinary 3D printer purchased off the Internet to combine a matrix of hydrogel and bovine cells with silver nanoparticles. Using CAD software, the printer deposits layer upon layer of gel, silver, and cells, building the ear out of an array of thin slices. The nanoparticles form a working antenna, while the cells multiply and mature into cartilage.
The finished product is soft and squishy and looks remarkably like the real thing, except there’s a coil antenna in the center. Two wires wind around its electrical “cochlea,” where sound is sensed. The wires can be connected to electrodes.
The ear is a step toward a device that someday could be used to restore a person’s hearing, or improve it by connecting electrical signals to a human’s nerve endings, as is customary with cochlear implants. But additional research and testing is being done. “The design and implementation of bionic organs and devices that enhance human capabilities, known as cybernetics, has been an area of increasing scientific interest,” the researchers wrote in an article. “This field has the potential to generate customized replacement parts for the human body, or even create organs containing capabilities beyond what human biology ordinarily provides.”
Revolutionizing Computing Architecture
As Princeton scientists chart a new course in the brave new world of cybernetics, Yale University scientists are inventing a new cyber age. Three Yale physicists are laying the foundation for the warp-speed computers of the future—machines that will harness the power of atoms and molecules to store, process, and transfer colossal amounts of data at almost unimaginable speeds, and do it in spaces so miniscule they cannot be seen by the naked eye.
Two applied physics professors—Robert Schoelkopf and Michel Devoret—are building a quantum computer, one “artificial atom” at a time. The scientists are putting “microwave quantum optics” on a chip by squeezing microwave photons, or tiny packets of light energy, into ultra small cavities on a chip. They’re also squeezing in electrical circuit elements, which act as artificial atoms that can be used as quantum bits, units that process and store quantum information.
These small “atoms” interact with the packets of light energy from the microwaves at extremely high speeds. The small cavity acts as a quantum bus of sorts, transmitting quantum information to and from the atoms. The result: a radical new architecture that may usher in the end of computing as we know it. Scientists hope to one day use this approach to create a huge integrated circuit of quantum bits, resulting in a quantum computer.
Old Fuel, New Production Method
Lehigh University researchers are looking to forge a new path in fuel production—creating a solution to the world’s unsustainable levels of energy consumption. They’re turning to the simple but powerful process most kids learn about in grade school, photosynthesis, to harness sunlight and synthesize liquid fuel from dissolved carbon dioxide.
While the process is new and extremely efficient, the fuel has been around for decades: it’s methanol, which is a safe fuel that burns cleaner than gas and can reduce hydrocarbon emissions by as much as 80%. In fact, methanol actually consumes CO2.
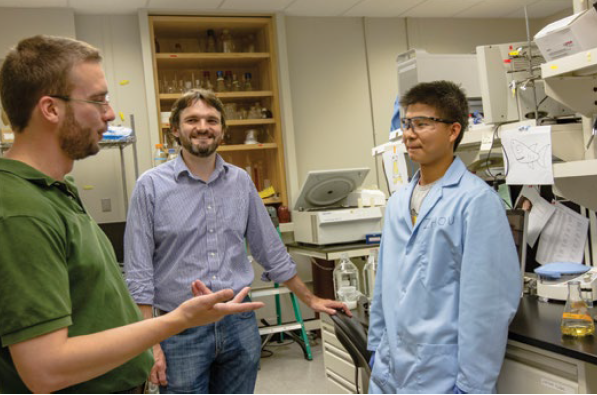
Methanol is mainly produced using natural gas or coal. Nobody knew it was possible to photosynthesize it into existence—until now. In the 1990s, methanol was marketed as an alternative fuel for vehicles. It was never fully adopted because there was no economic incentive for continuing methanol production as petroleum fuel prices fell in the ‘90s.
Why turn to methanol again? Because it has a higher-octane level than gasoline, there are no technical hurdles for vehicle design and fuel distribution, and a methanol-based fuel economy would dramatically reduce energy dependence on dwindling fossil fuel sources.
Converting Sunlight into Methanol
By using a cross-disciplinary effort in catalysis, materials chemistry, and cellular engineering, Lehigh scientists have found a way to directly convert sunlight into methanol, bypassing the need to grow and process a plant.
The team replaced slow, natural photosynthesis with rapid, efficient, and selective artificial photosynthesis, using semiconductor quantum dots (QDs) as photocatalysts. QDs are nanocrystals that once promised to revolutionize display technologies, solar power, and biological imaging. A key barrier has been price; they cost up to $10,000 per gram, thus their use has been limited to special applications.
The Lehigh team discovered a novel way to produce QDs: by using an engineered bacterial strain to initiate and control their growth—essentially a batch fermentation process. “We are thus able to achieve a cost of less than $38 per gram for quantum dots,” says Bryan Berger, professor of chemical engineering and co-principal investigator.
The Lehigh team has projected production costs for their methanol to be 65% cheaper than current costs for producing biodiesel fuel. If they can develop a production method that can be scaled-up and is commercially feasible, photocatalytic methanol production could have a significant long-term impact on society and the economy.
“A low-cost, green fuel produced in large quantities from carbon dioxide, sunlight, and water could potentially meet our transportation needs. It would reduce oil imports without depleting our natural resources,” says Berger.
New Diagnostic Tools Target Tumors
The University of Pennsylvania (UPenn) technically sits outside the New York tri-state area and yet its extraordinary commitment to R&D (as exemplified by an annual budget of more than $800 million) and a legacy of discovery traced to Benjamin Franklin, the Founding Father with a knack for creating something out of nothing, makes it an important contributor to the region’s science ecosystem.
While UPenn created the first general-purpose electronic computer in the early 1940s, a 27-ton, 680-square-foot model that calculated ballistic trajectories during World War II, current UPenn scientists are leading explorers in the world of the infinitesimal. By developing nanotechnology as an effective diagnostic tool, researchers are hoping to revolutionize the prevention and treatment of disease.
While magnetic resonance imaging (MRI) can produce topographical maps of tissue, scan clarity isn’t always sufficient for diagnosis. To mitigate patients’ health risks and to improve imaging, UPenn researchers are coating an iron-based contrast agent so it interacts with the acidic microenvironments of tumors, making tumors stand out clearly from healthy tissue. The approach is both safer and less costly than other methods.
The coating of glycol chitosan—a sugar-based polymer that reacts to acids—allows nanoparticles to remain neutral when near healthy tissue but to become ionized in low pH. In the vicinity of acidic tumors, a change in charge causes the nanoparticles to be attracted to and retained by the tumors.
Delivering Drugs to Tumor Sites
“Having a tool like ours would allow clinicians to better differentiate the benign and malignant tumors, especially since there has been shown to be a correlation between malignancy and pH,” says Andrew Tsourkas, associate professor of bioengineering. The coated nanoparticles are not limited to imaging, he added. “They can also be used to deliver drugs to tumor sites.”
Developing Infection-Resistant Medical Implants Scientists at Stevens Institute of Technology are developing next generation, bacteria-resistant biomaterials that could become an implant staple for millions of patients. And as the population ages, the market for orthopedic implants will experience exponential growth; by 2017, the global market will reach $46 billion. But 1% of hip implants, 4% of knee implants, and 15% of implants associated with orthopedic trauma fail—due to infection.
“Usually the only way to resolve a biomaterials-associated infection is to remove the device, treat the infected tissue, and later implant a second device,” says Matthew Libera, professor of materials science at Stevens. “Not only does this bring really significant cost to the healthcare system; it forces the patient to undergo a lengthy and challenging surgical and rehabilitation process. We would like to eliminate that risk.”
Stevens faculty from numerous disciplines, including materials science, chemical biology, and biomedical engineering, developed technology that actually repels bacteria and promotes the growth of healthy bone cells on uncemented implants. The surface of the implants is treated with hydrogel because most bacteria, particularly the staphylococci common to implant infection, do not adhere to most hydrogels. As a result, patients won’t have to take antibiotics orally; the medicine will go to work at the surface of the implant.
A Local Home for the World’s Biosamples
Many of the biospecimens used in research projects across the region, and around the world, are provided by Rutgers University, a national leader in genetics. RUCDR Infinite Biologics, founded in 1998 as the Rutgers University Cell and DNA Repository, is the world’s largest university-based biorepository. It provides DNA, RNA, and cell lines with clinical data to research laboratories worldwide, which use them to study a host of diseases and disorders.
RUCDR contains more than 12 million biosamples, logs 100 million database entries per year, operates one of the nation’s largest stem cell programs, and facilitates a slew of research initiatives.
“This sort of advanced-technology, automated facility was sorely needed on the national level, and we anticipate a continual increase in use by Rutgers faculty,” says RUCDR CEO Jay A. Tischfield, director of the Human Genetics Institute of New Jersey and professor of genetics.
Last year, the repository received a $10 million grant from the National Institute on Alcohol and Alcoholism Abuse to provide DNA extraction, basic genetic testing, and repository services for more than 46,000 saliva samples for a national research effort to determine the genetic and environmental factors leading to alcoholism. Formerly, large-scale studies on the causes of alcoholism used sociological, behavioral, and limited biological data.
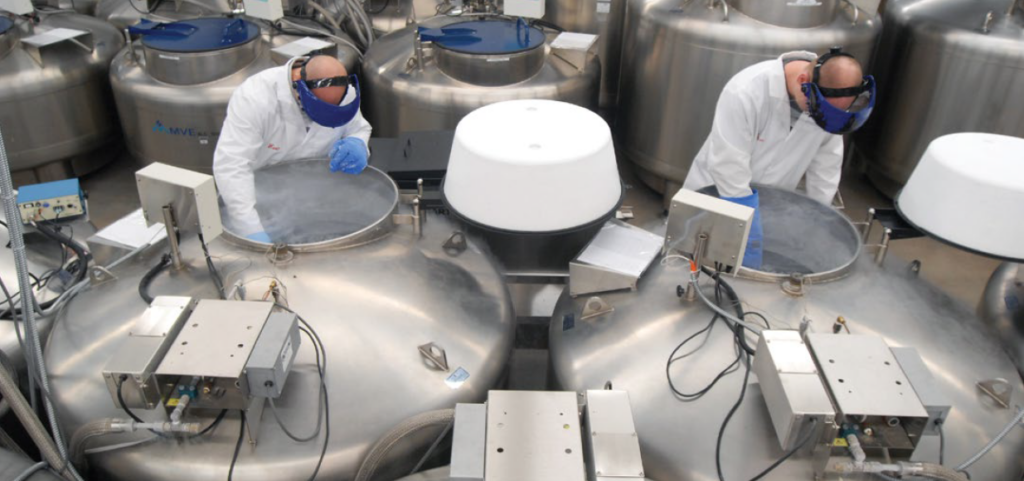
Robust Epidemiological and Biological Information
“For the first time, researchers will have robust epidemiological and biological information from large numbers of individuals so that they may correlate genetics to alcohol abuse behavior,” Tischfield says. “The results are used to formulate national policy and improve healthcare services.”
In 2013, RUCDR received $44.5 million from the Cooperative Agreement award from the National Institute of Mental Health (NIMH), which will allow RUCDR to support the NIMH Center for Collaborative Genomics Research on Mental Disorders by collecting, processing, and analyzing blood and tissue samples from NIMH-funded scientists nationwide.
“With the new funding, RUCDR Infinite Biologics will implement new meta-analytic approaches for combined analysis of clinical and genetic data in the NIMH Human Genetics Initiative,” says Tischfield.
Transforming Lives through Research
Research projects such as those detailed above represent just a fraction of the novel endeavors under way in labs across the tri-state region—probing mysteries that puzzle us, creating technologies that amaze us, and making discoveries that alter how we live and think. And in the process, Tri-State scientists are bringing robust new revenue streams to the local economy—creating both short- and long-term benefits.
While we may never see a plastic twin of the George Washington Bridge, plastic bridges are on the horizon, literally. Rutgers has partnered with the U.S. Army Corps of Engineers to build plastic lumber bridges that can tolerate punishing loads: 70-ton tanks and 120-ton locomotives.
Chances are, structural plastic has already touched your life. If you’ve ever traveled by train, you have probably glided along rails held in place by plastic railroad ties. With 212,000 miles of track in the U.S., ties are big business; 20 million are replaced each year for maintenance, and composite ties are rapidly gaining notice for their corrosion-resistance.
Leave it to scientists in the tri-state region to come up with an ingenious idea for what to do with the world’s rubbish: create everlasting building blocks.
Steven Barboza is a writer in New Jersey.
This story originally appeared in the special 2013 edition of The New York Academy of Sciences Magazine.
Also read: Two New York Startup Companies Envision a Waste-Free Future